Обжиг цементного клинкера при
нагревании в неравновесных условиях
Создать неравновесные условия
можно следующими способами:
- резкий обжиг;
- обжиг укрупненного помола
шлама;
- двухшихтовая технология.
Рассмотрим каждое из приведенных
условий.
1. Резкий обжиг клинкера – очень
быстрое нагревание при вводе материала в разогретый до максимальной температуры
реактор. В этом случае обжиг клинкера идет с максимальной скоростью. Данный способ
может быть осуществим только при производстве цемента по «сухому способу», т.к.
после декарбонизации и подогрева сырья в запечных теплообменниках сырьевую муку
можно сразу подать в зону с максимальной температурой. При «мокром способе»
этот процесс не осуществим, потому что материал нагревается постепенно, проходя
по всей длине печи.
Рассмотрим график зависимости
времени обжига от температуры (рис.1):
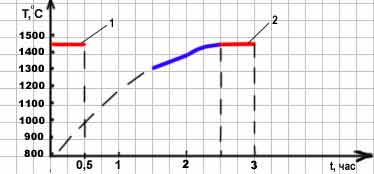
Рис. 1
На графике видим, что процесс обжига
длится всего 0,5 часа при резком обжиге (2), при постепенном обжиге время самого обжига так
же 0,5 часа. Все остальное время, 2,5 часа необходимо для нагревание материала
до образования расплава.
Многократное ускорение процесса
обжига объясняется следующим:
1) Ускоряются процессы разложения
СаСО3 и глинистых материалов и совмещаются во времени с синтезом
оксидных минералов (силиката, алюмината и феррита кальция). Реагирующая фаза
находится в высокодисперсном состоянии и с большим числом дефектов, что
обеспечивает высокую химическую активность.
2) При резком обжиге образуется
дополнительное количество высокосиликатного расплава, обладающего пониженной
температурой плавления (1130-1180 ºС, в отличие от 1338 ºС при постепенном
обжиге). Этим и доказывается физико-химическая
интенсификация процесса обжига клинкера в неравновесных условиях. Синтез
происходит в 5-6 раз быстрее чем при длительном нагревании.
При постепенном обжиге происходит
спекание оксидов и только потом, при 1338 ºС их плавление:
С + S --> C2S --> CS --> C2S --> C3S
C + A --> CA --> C12A7 -->C3A
C+F --> CF --> C2F
При резком обжиге происходят
следующие реакции:
С + S --> C2S
C + A --> CA
C+F --> CF
Оксиды C2S, CA, CF
образуются при резком обжиге без спекания, температура их плавления 1130-1180 ºС,
поэтому расплава больше и при более низкой температуре.
Химический состав расплава:
С – 45%
А – 10%
F – 8%
S – 37%
Минералогический состав расплава:
- железосодержащий геленит (C2AS) – 26%
- железосодержащий волостонит (α-CS) – 74%
Колмчество расплава при резком
обжиге – 50-55%, количество CaO
– 50-45%. Меняется механизм и последовательность образования клинкерных
минералов:
α-CS (F) + CaO --> C2S
+ C3S;
C2AS
(F) + CaO --> C3S
+ C3A + C2F
Количество расплава контролируемо
и определяется скоростью реакции и температуры. Процессы рекристаллизации и
спекания отсутствуют.
На практике распространения пока
не получили, но аппарат для резкого обжига недавно был создан японскими
специалистами. Аппарат состоит четырех циклонных декарбонизаторов и реактора, представляющего
собой конструкцию кипящего слоя.
Холодильник для охлаждения клинкера так же выполнен в виде кипящего слоя.
Процесс обжига в таком аппарате длится всего 6-8 минут, гранулы клинкера имеют
размер 1,5 – 3,5 мм.
В скором будущем резкий обжиг
клинкера во всем мире будут производить именно в таких реакторах кипящего слоя.
2. Обжиг укрупненного помола
шлама (по карбонатному компоненту, 30% остатка на сите №008)
На рис.2 изображена частица CaO, взаимодействующая с расплавом. По мере
взаимодействия с расплавом на поверхности частицы образуется
высококремнеземистый слой 2, который постепенно проникает внутрь частицы,
уменьшая радиус еще не прореагировавшего CaO 3. Вокруг частицы CaO находится высокодисперсные частицы
глины 1 без примесей. Диаметр частицы СаО примерно 150 мкм.
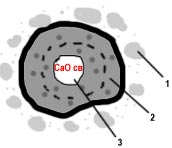
Рис. 2
В центре остается свободный СаО,
не успевающий прореагировать. В этой системе неравновесность представлена
крупными частицами карбоната. При 1130 – 1150 ºС пленка плавится и пропитывает
центр зерна, идут процессы синтеза клинкерных минералов. Синтез идет до конца,
если количество крупных частиц, не прошедших через сито №008 не более 30%.
Синтез идет по той же схеме, что при резком обжиге. Образуются только
низкоосновные силикаты кальция из-за недостатка СаО. Если частиц больше 30% и
их размеры больше, то в клинкере остается более 1% СаО свободного, что приводит
к разрушению готового изделия в следствии гидротации СаО в затвердевшей массе.
Данный метод используется на
практике Старооскольским цементным заводом.
3. Двухшихтовая технология
Двухшихтовая технология
заключается в приготовления шлама в виде двух шихт:
-
легкоплавкая
шихта 1;
-
шихта II
(карбонатный компонент).
Схема приготовления следующая:
мел - 78%
глина - 20%
огарки – 2%
отнимаем 50% карбонатного
компонента, останется:
мел – 28% |
глина – 20% |
- шихта 1;
огарки – 2% |
мел – 50% -
шихта 2.
Обжиг производится во вращающейся
печи методом двухстороннего питания. Шихта 2 подается с холодного конца печи, с
влажностью 40%. Шихта 2 подается с горячего конца печи через специальную
форсунку с потоком воздуха под давлением. На рис.3 схематически изображен способ
обжига методом двухстороннего питания.
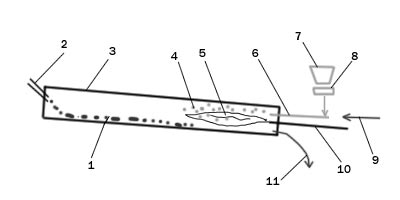
Рис. 3. 1-слой карбонатного компонента (шихта 2), 2 - шламовый питатель, 3- корпус вращающейся печи, 4- капли легкоплавкого расплава, 5 -факел сгорающего топлива, 6- труба для подачи шихты 1, 7- бункер шихты 1, 8 - дозатор, 9 сжатый воздух от коипрессора, 10 подача топлива, 11 - выход клинкера.
Этот метод имеет следующие
достоинства:
- экономия топлива 25%;
- более высокое качество клинкера
за счет микрокристаллической структуры;
- уменьшение потерь тепла
корпусом.
Опыт использования такого метода
обжига клинкера имеется. Но здесь так же имеются трудности. Эта трудность
заключается в подаче шихты с горячего конца печи посредством отдельной трубы.
На конце трубы, находящемся в печи имеется форсунка, через которую производится
подача материала. Через эту форсунку очень трудно подать 50% сырья (шихта 1)
вследствие относительно низкого давления (для больших печей масса шихты 1 достигает
75т/ч). Таким образом, чем больше твердой фазы будет в воздушном потоке, тем
больше будет трение воздушно-пыльного потока о стенки форсунки, концентрация
пыли достигает 4-5 кг/м2. Если увеличить давление воздушного потока,
то можно охладить зону обжига и тем самым увеличить расход топлива, что не приемлемо.
Обжиг цементного клинкера при
нагревании в неравновесных условиях будет очень перспективным в скором будущем.
Эти методы постоянно изучаются и совершенствуются, достигая высокой
эффективности. На данный момент обжиг при нагревании в неравновесных условиях
мало распространен на практике, в следствие затруднений в инженерном воплощении
идей.
|